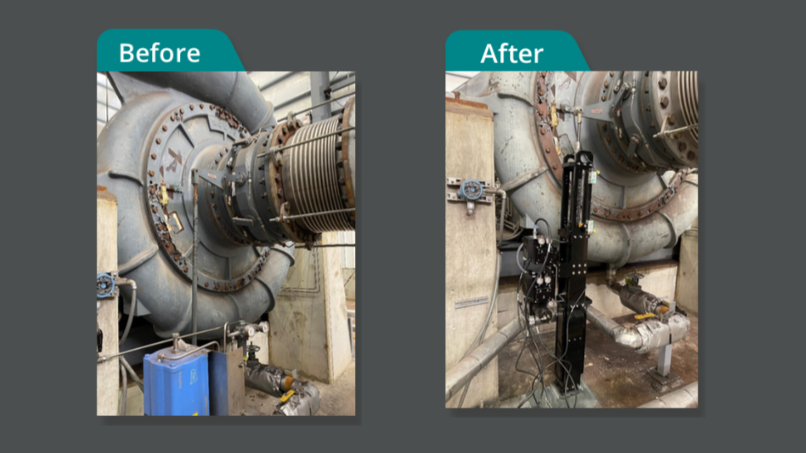
CASE STUDY: PROCESS GAS COMPRESSOR FLOW CONTROL FOR HBI PRODUCTION
In 2020, the largest North American producer of flat-rolled steel, completed a new direct reduction plant. The plant produces hot briquetted iron (HBI), a versatile iron source needed to produce steel in electric arc furnaces, basic oxygen furnaces, and blast furnaces. The plant has a closed loop gas circuit that dedusts, compresses, and reheats the gas. Natural gas is also added to the loop. To achieve the highest quality HBI product, optimum process control of product temperature and furnace atmosphere is required.
In May 2021, the direct reduction plant’s HBI pellets were transferred to their sister company’s blast furnace. In the blast furnace, the HBI blends with coke and iron ore additions. Iron ore (largely Fe2O3) is rich in iron oxides which are reduced by carbon monoxide to form elemental iron and carbon dioxide. Not only are carbon dioxide emissions reduced using HBI on blast furnaces but also the blast furnaces run more efficiently. Four months into the HBI pellet production, the plant’s operations group had grown increasingly frustrated with their pneumatic actuators.
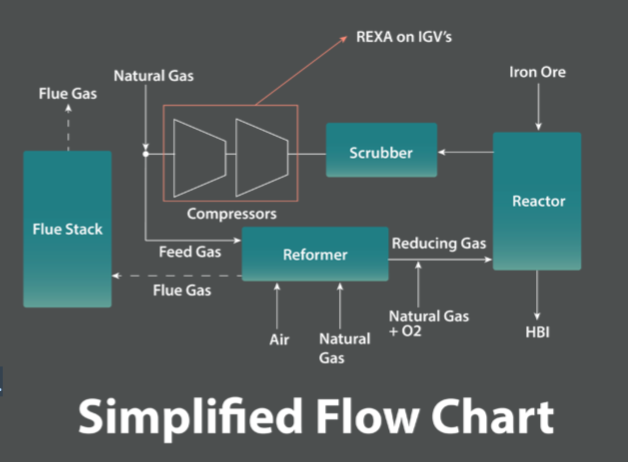
The actuators were doing an inadequate job of positioning the compressor inlet guide vanes (IGVs). Accurate positioning of each compressor on the IGVs is necessary to precisely control the gas throughput, with two compressors in series. Doing this effectively ensures optimal gas flow through the compressor. The compressor IGVs uses a pneumatic rotary actuator. During start-up, the pneumatic actuators had one second delays before moving to position. The slow and inaccurate positioning led to terrible vibration, causing the compressor to shut down. In some cases, up to six manual attempts were tried before the process could restart.
In May 2022, both compressor IGV’s were upgraded with a REXA ElectraulicTM linear actuator. REXA supported the upgrade by providing a site survey, engineering drawings, and onsite start up commissioning. Plant personnel immediately noticed improved repeatable accuracy to 0.1% of span, regardless of process conditions. The REXA actuators have the capability to open from 0-20%, in under two seconds, without overshooting. For this reason, the plant can now safely start up the compressors without vibration.
“REXA provided the benefit of automated startups without
failures and improved process control allowing the tuning for HBI product chemistry.” - Instrumentation and Controls Engineer
Return on Investment:
• Annual HBI production is 1.9M tons, equivalent to $16,000 per hour.
• Compressor restart time delays, that result in HBI production loss, costs ~$96,000 per day of repeated start up attempts.
• For two actuators, REXA payback is < 1 year.
The process gas stability has also improved, leading to better control of the HBI product chemistry. By utilizing REXA actuators, the steady-state process gas flow oscillation was reduced from +/- 2,000 m3/hour to +/- 50 m3/hour. Other benefits of improved process control are the reduction in natural gas consumption and less modulating of the 24 downstream control valves. In turn, the control valves’ maintenance intervals were extended.
Producing and using HBI contributes to the steel company’s greenhouse gas reduction initiative. REXA actuators contributed to improving the HBI plant operations with improving process gas stability.
Source: rexa.com